戦闘機材料開発
お話した様に、初めからいきなり戦闘機用の材料開発を担当(チタン合金の世界ではある意味王道なのですが)することになり、それはそれでやり甲斐もあり、充実した仕事では有りましたが、FSXの開発については米国から「日本に第2のゼロファイター(零戦)を造らせるな!」という激しい横槍(後に本にもなりましたが)が入り、時のクリントン政権と、米国製F-16をベースに、使用するチタン合金部品も米国製とすると日本政府が合意した事から、当初15アイテムあったチタン合金鍛造部品の内、住友金属で製造する物は1アイテムのみになってしまいました。
F-16 F-2
その他の部品についても、当時画期的であったCFRP(炭素繊維強化プラスチック)製の主翼についても無償で技術提供させられたと記憶しています。開発を担当したのは、主翼と尾翼を胴体に繋げる部品で、Ti-10V-2Fe-3Al(通称:1023)いう成分系のnearβ型チタン合金製でした。この1023という材料が曲者で、特に成分中の Fe がとても偏析しやすいため大きなインゴットを製造するのが難しく、均質にするためには1ton程度に重量を抑える必要がありました。
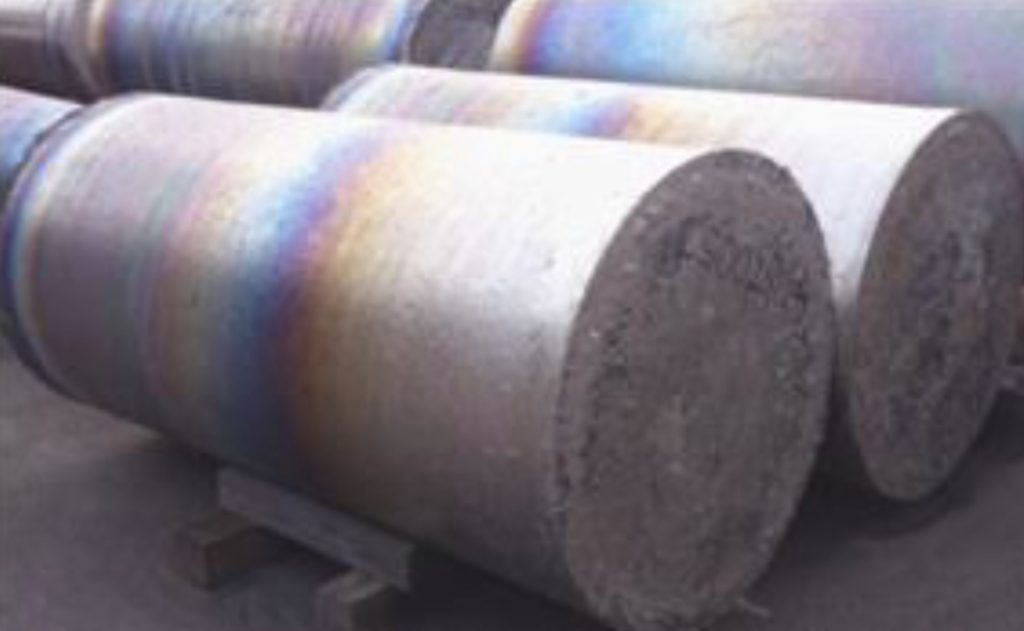
その後、鍛造して型鍛造用のビレットと呼ばれる形状にし、恒温鍛造と言う手法で型鍛造するのですが、当初どうしても要求される特性の内、破壊靭性という特性を満足させる事が出来ませんでした。破壊靭性とは、部品に亀裂が生じた場合完全に破壊されるまでどれだけ耐えられるか?を示す指標になりますが、この部品の特性(戦闘機の胴体と翼を繋げる)上、様々な方向からの亀裂に耐える必要がありますが、ある一方向のみどうしても仕様を満たしませんでした。なぜ満たさないのかを調べていくと、最後の型鍛造後の組織を観察した結果、金属組織の流れを示すメタルフローと破壊靭性試験時の亀裂方向の関係に大きな相関がある事、最終熱処理工程後の析出層の大きさにも相関がある事が判りました。そこで、当時は未だコンピューターシミュレーションもあまり発達していなかったので、粘土(正確にはプラスティシンという特殊な粘土)を色違いにして層状に重ね、様々な方向から押してみてその層変化を観察してメタルフローの改善に取り組みました。また析出層の改善(正確には時効析出層の改善)には、時効処理前の溶体化処理時の冷却速度にカギがある事が判り開発に取り組みました。しかし、なかなか理想の冷却速度が実現出来ず、色々な冷却媒体(中には腐ると異臭を放つ物もあり、鼻を摘んで作業した事もありましたが)を試しましたが、結局はお湯につけるのが一番という結論でした。
余談ですが、熱処理試験の思い出として、生まれて初めて救急車に乗った事を思い出します。徹夜続きで体調が悪い中、早朝の作業中に耐えられなくなり会社の診療所に行った所、手脚の痺れが酷くなってきた為、救急車で大きな病院に運ばれました。そこで息が粗くなっているのを見た若い看護師さん(当時は看護婦さんと呼んでましたが)が、酸素マスクを着けてくれたのですが、益々痺れが強くなり失神状態になりました。そこにベテランのお医者さんが入ってきて「過呼吸の患者に酸素マスク着けてどないするねん!」と一括するや、酸素マスクを外して近くにあった紙袋を筆者の顔に被せ、「しばらくほっといたら治る」と言い放って出て行きました。確かに数分で楽になり、点滴の効果もあってか数時間後にはかなり回復しました。夏の暑い時期、あまり水分もとらずに熱処理なんかしてたもんですから、今から思うと熱中症だったんだと思います。
そんな苦労もありながら、なんとか特性も仕様を満足する様になり、結果的にはユーザーさんから「素晴らしい部品をありがとうございます」と言われた時は、苦労した甲斐があったなとしみじみ思いました。